The Simulation of Gas Film Flow Field in Aerostatic Thrust Bearing
Abstract
Based on the CFD software, the numerical simulation and visualization of the gas flow in the gas film gap are carried out. Considering the influence of gas flow, the laminar flow model was adopted when the clearance is relatively small and a realizable model was adopted for large gaps. This research analyzes the effect of bearing clearance on gas pressure, velocity and Mach number, and accurately captures the flow field characteristics of the bearing inlet region. The calculation results show that the inlet gas film pressure drops significantly or even lower than the ambient pressure under large clearance conditions, so the influence of inertial force cannot be ignored. The mechanism of pressure drop and recovery is revealed by the theory of expansion wave and compression wave for the phenomenon of shock wave near the entrance.
References
Gupta, R. S., & Kapur, V. K. (1982). Inertial effects on pressure depression in gas-lubricated thrust bearings. Wear, 77(2), 203–206. https://doi.org/10.1016/0043-1648(82)90104-1
Mori, H. (1961). A theoretical investigation of pressure depression in externally pressurized gas-lubricated circular thrust bearings. Journal of Basic Engineering, 83(2), 201–208. https://doi.org/10.1115/1.3658925
Mori, H., & Miyamatsu, Y. (1969). Theoretical flow-models for externally pressurized gas bearings. Journal of Lubrication Technology, 91(1), 181–193. https://doi.org/10.1115/1.3554854
Poupard, M., & Drouin, G. (1973). Theoretical and experimental pressure distribution in supersonic domain for an inherently compensated circular thrust bearing. Journal of Lubrication Technology, 95(2), 217–220. https://doi.org/10.1115/1.3451775
Shih, T. H., Liou, W. W., Shabbir, A., Yang, Z., & Zhu, J. (1995). A new k-ε eddy viscosity model for high Reynolds number turbulent flows. Computers & Fluids, 24(3), 227–238. https://doi.org/10.1016/0045-7930(94)00032-T
Yang, J.-F., Chen, C., & Han, D.-J. (2012). Rotor-bearing system fluid-solid interaction and frequency modulation technology. Journal of Vibration and Shock, 31(S), 281–285.
Yoshimoto, S., Yamamoto, M., & Toda, K. (2007). Numerical calculations of pressure distribution in the bearing clearance of circular aerostatic thrust bearings with a single air supply inlet. Journal of Tribology, 129(2), 384–390. https://doi.org/10.1115/1.2464135
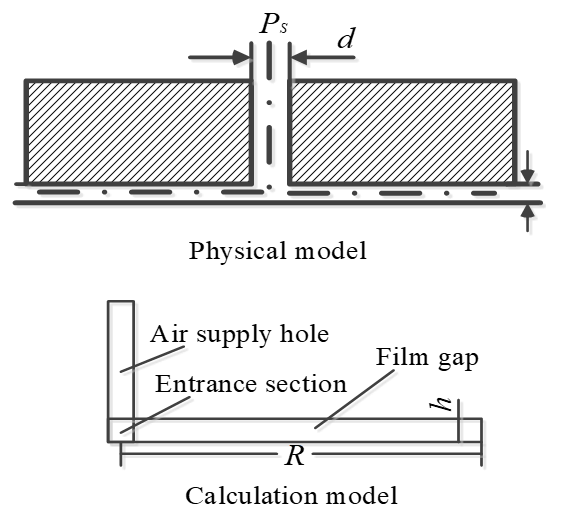

This work is licensed under a Creative Commons Attribution 4.0 International License.
Copyright for this article is retained by the author(s), with first publication rights granted to the journal.
This is an open-access article distributed under the terms and conditions of the Creative Commons Attribution license (http://creativecommons.org/licenses/by/4.0/).